5.2.1.6 Thickness
The thickness of the substrate may also be indicative of the interaction between the substrates and the adhesives. Even a material with a high modulus (i.e. rigid materials like aluminium) can become very flexible in thin films or sheets. A good example is aluminium foil commonly used for cooking. It is easily folded or torn by hand, compared to a thick plate or sheet of aluminium, which requires mechanical force to fold or tear. Differences in test data and the real world may at times be explained by this property, as real-world test data on thinner or thicker substrates may differ from the numbers provided in technical literature such as the TDS (which is calculated using standard dimension substrates).
For example, thinner substrates will sometimes induce different failure modes, commonly transforming a shear or tensile adhesion failure into a peel failure, as the thin substrate deforms. Another failure mode that can occur in testing with thin materials is substrate failure, in which a test specimen fails before the adhesive joint due to insufficient substrate thickness. While substrate failure can be a desirable failure mode because it confirms the ability of an adhesive to outperform the material it is bonding, data from materials property testing will reflect the strength of the substrate and not necessarily the adhesive.
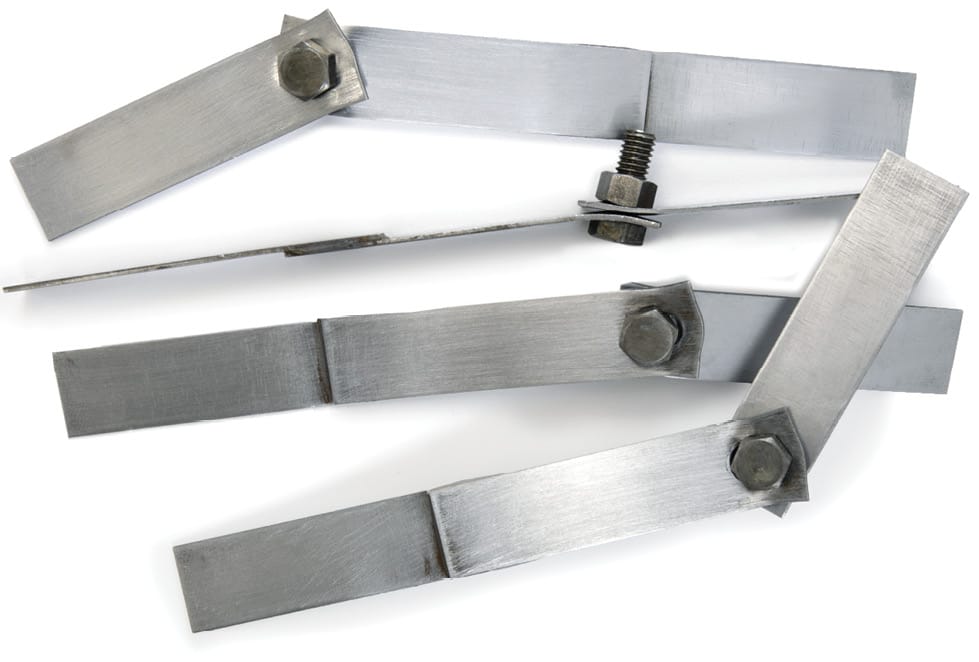
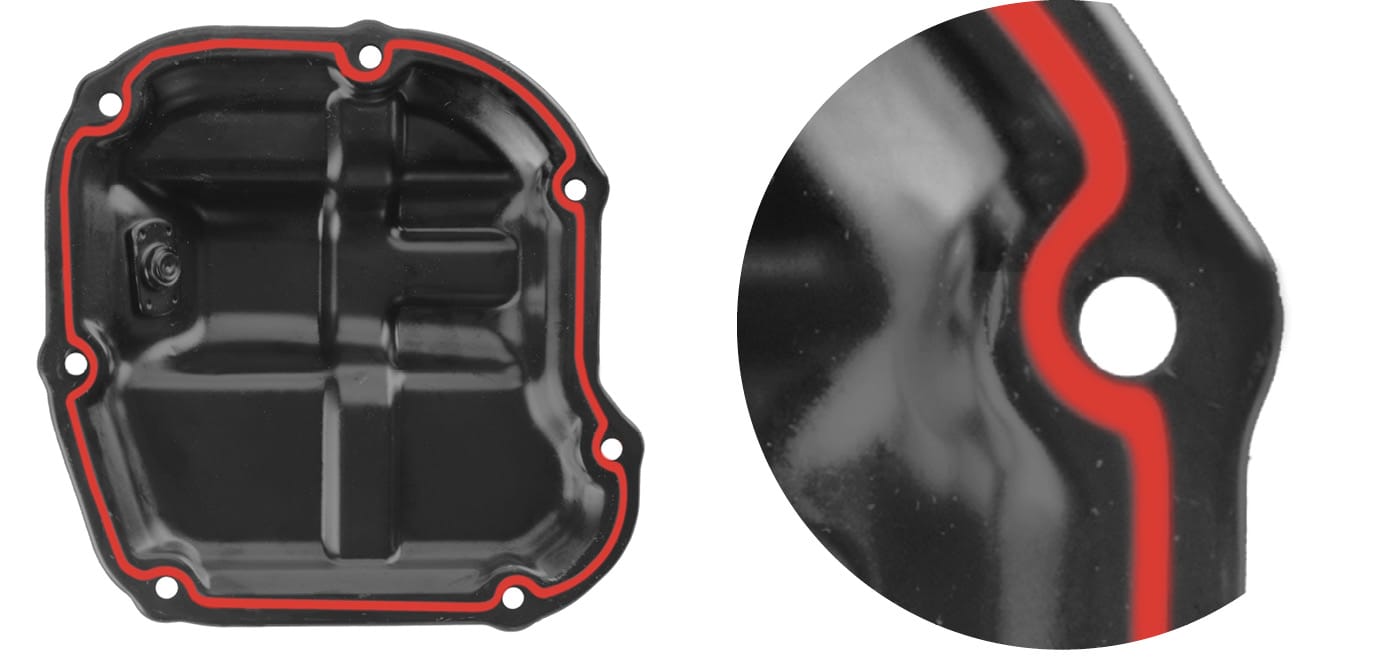
The flexibility of the substrate as it decreases in thickness is prevalent when comparing rigid flanges and stamped flanges, both of which are sealed by compressing an elastomeric adhesive and which may lose their ability to form a reliable seal if the flange material, in this particular case a rigid flange (cast metal), is too thin. An excess clamp load on the stamped flange may lead to deformation, allowing a leak path. A rigid flange (cast metal) generally does not see this issue. Flexibility as it relates to material thickness explains why stamped parts have greater stress concentrations than thicker machined flanges.
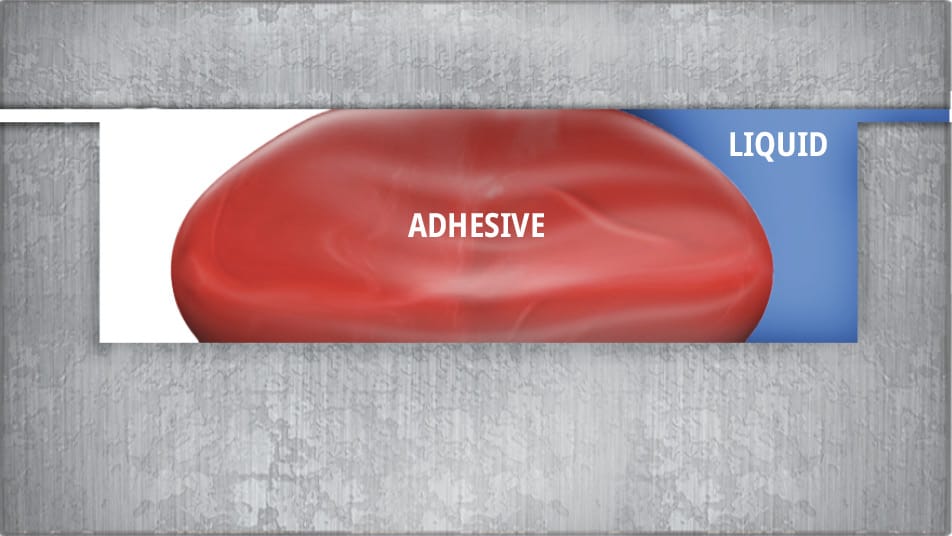