4.2.1 Operator Training
A key factor to consider when addressing bonding applications is the education and training levels of the adhesive user or operator. It is important to understand how to design components for adhesive bonding and bring them effectively to production; however, the workers in production must also be trained on how to handle adhesives and complete bonding applications. While applicator training is required for many applications and processes, adhesives training for workers is often offered by the adhesive supplier as a no-charge, value-added service.
Companies that select adhesives consistently for key projects or use them to manufacture numerous products benefit from having highly skilled adhesive specialists at their disposal. The collaboration between design engineers and relevant specialists can maximise the performance, effectiveness, efficiency and quality of production processes and the final bonded assembly. Adhesive joining contrasts with many alternative joining methods (i.e. welding), where the cost to train applicators (employee time), hire qualified staff or retain skilled labourers or tradespersons is significantly higher. This is particularly important in markets with difficulty retaining skilled labour due to high wages and high demand.
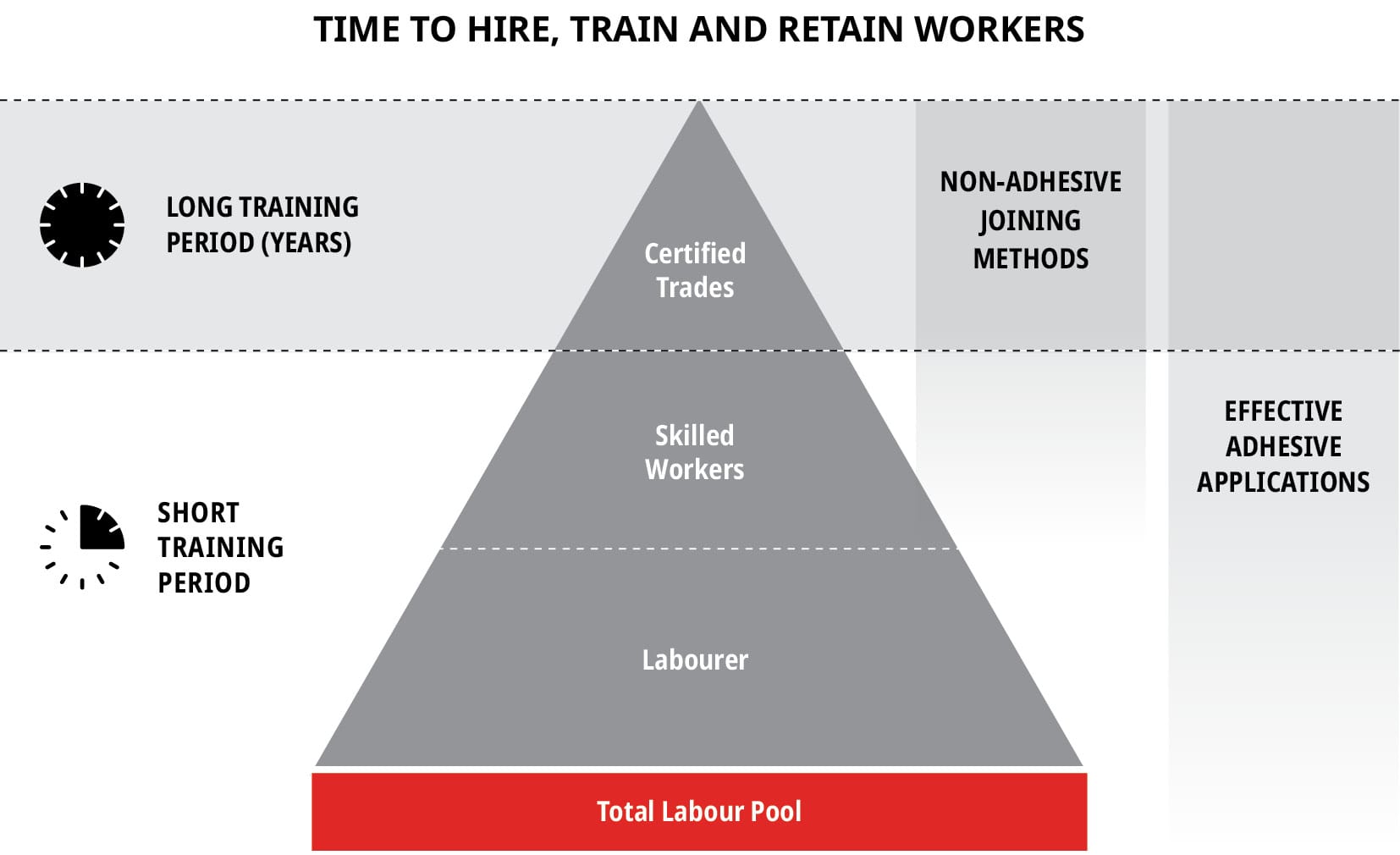
Training is important due to an increasing number of industry standards requiring operators to have specific qualifications in handling adhesives from both a health and safety and a quality perspective. This addition is already part of many quality management systems and will become more critical in the future. As with any joining method, a suitable design and correct material specification can be nullified by improper use and application of the product, resulting in variable performance or even failure during operation. Therefore, training, education and quality control are vital for all aspects of joining and manufacturing. Adhesives offer a distinct advantage over other joining methods due to the ease and speed of training operators.
As mentioned previously, many manufacturing and assembly processes are currently in use. Such processes and factors must be considered when selecting an adhesive. There may be speed limitations, process limitations and health and safety factors to consider before selecting an adhesive for a given application.