5.2.1.3 Substrate Flexibility
In general, many adhesives will have properties relating to flexibility listed in the technical literature, such as TDS or material specification sheets. The flexibility of cured adhesives will usually be characterised by Young’s modulus (also referred to as the elastic modulus), elongation before break and Poisson’s ratio. In general, there is a trade-off between shear strength performance and elongation, as seen in Figure 127. Engineers must be aware of this relationship when they match the flexibility of the adhesive to the requirements of the surfaces being assembled. Just like solid materials, cured adhesives have flexibility and strength properties that vary by polymer chemistry. Generalised expected properties by chemistry are shown in Figure 127. In many cases, matching the flexibility of the adhesive to the substrate (Figure 128) is ideal. In other cases, a high-strength, rigid bond is required to provide the best structural integrity.
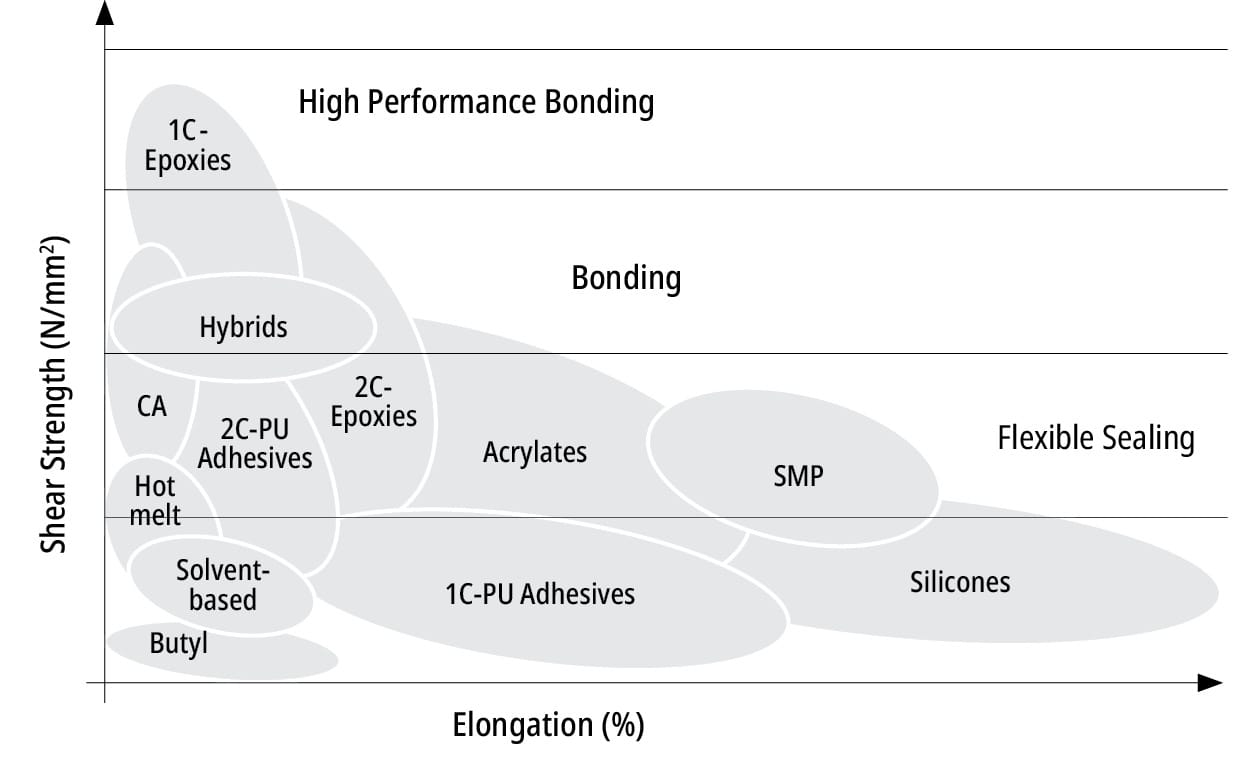
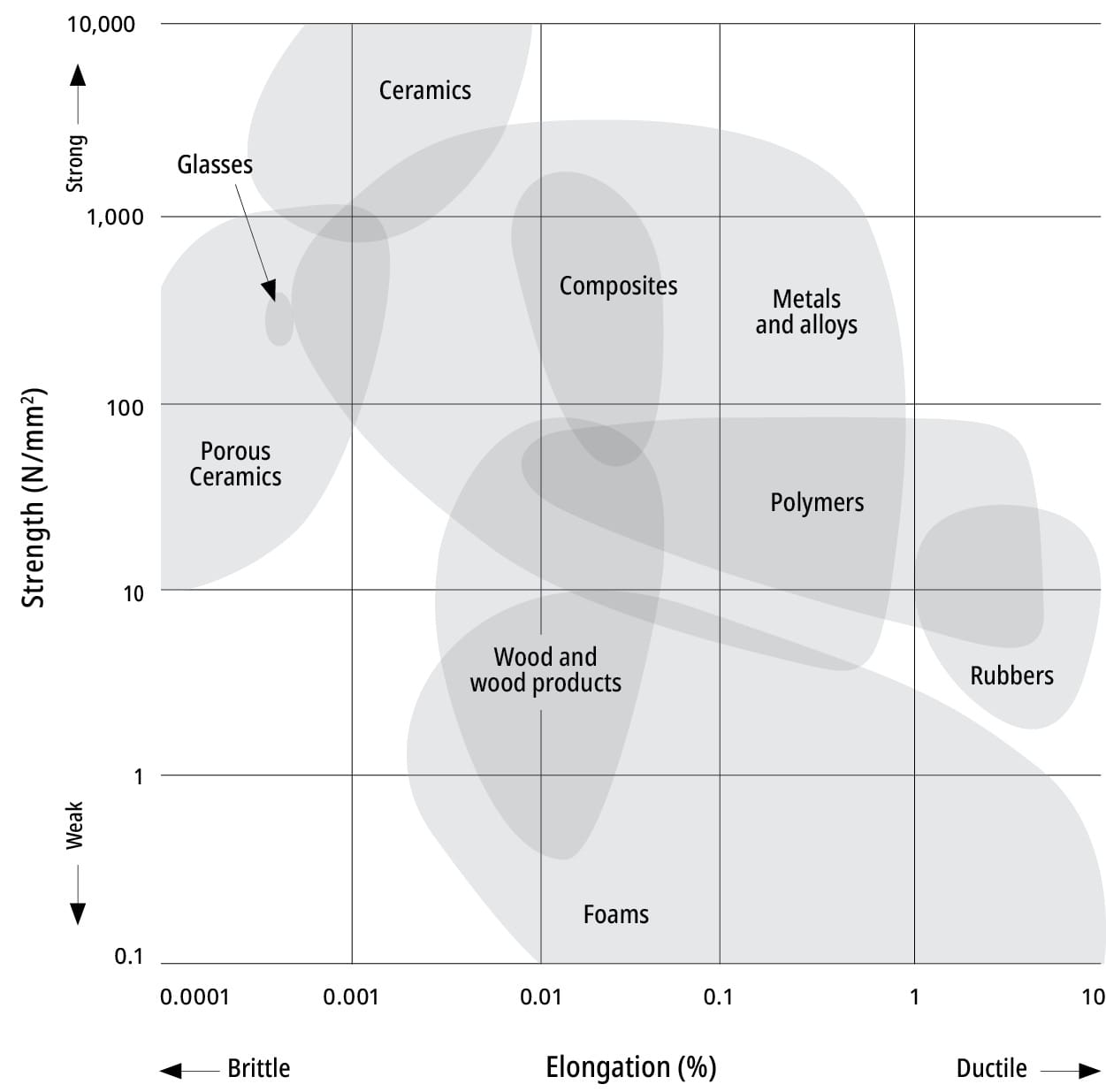
All solid materials will also exhibit many of the same properties as cured adhesive. The flexibility specification of many common materials is available in online databases or is readily available from manufacturers. In most cases, adhesives are more flexible, with a much lower Young’s modulus, than the materials to which they are bonded. However, adhesives are sometimes used to stiffen thin, flexible substrates in conjunction with a solid composite ‘honeycomb’.
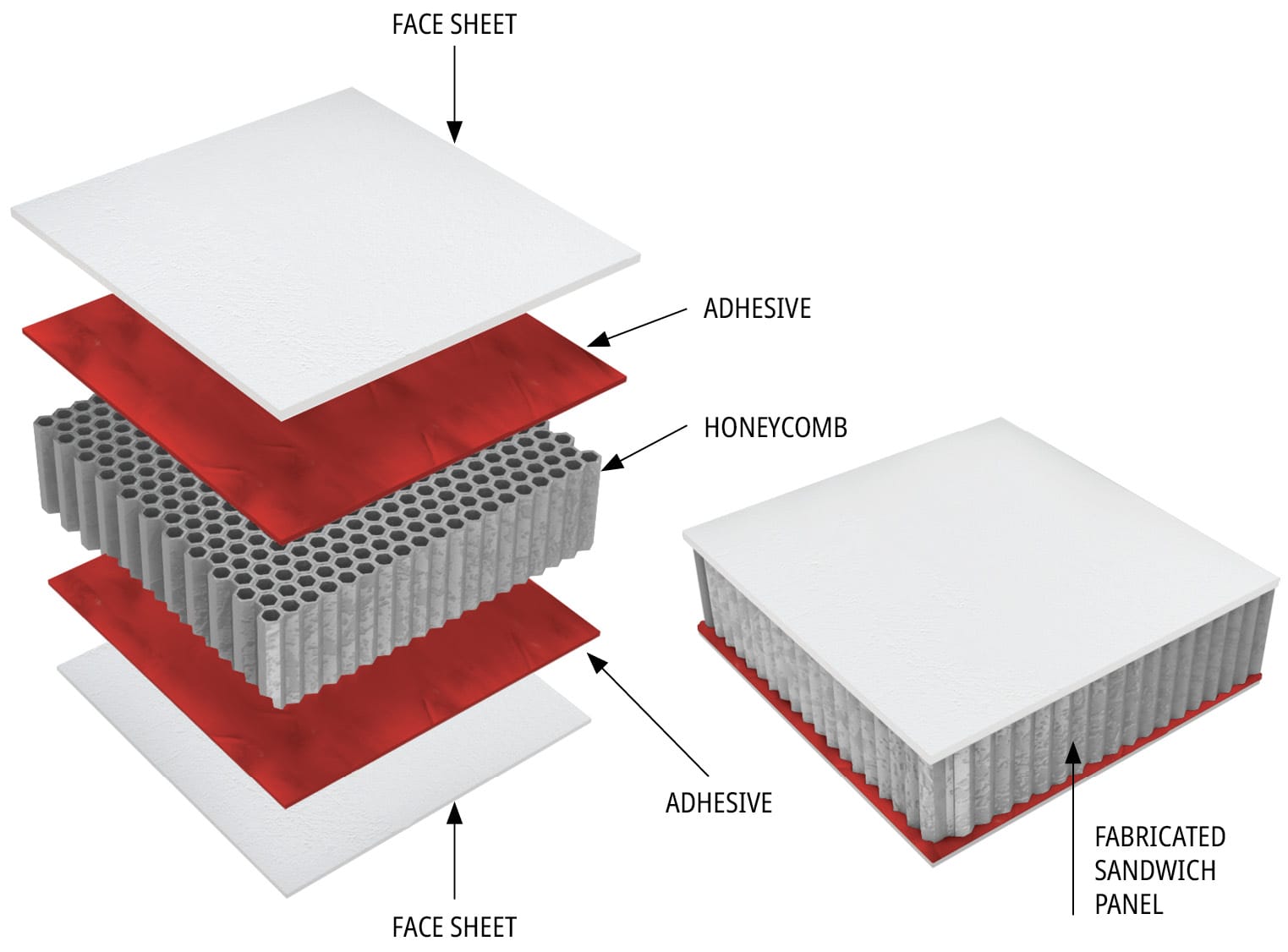
Depending on the expected static or dynamic loads to which an assembly might be subjected, it may be necessary to use a more flexible adhesive to accommodate microscopic displacements of surfaces, which may lead to cracks/failure in more brittle substrates. A common misconception is that a higher frequency or magnitude of dynamic loads should be addressed by selecting adhesives with higher shear strengths, when, in many instances, high magnitude or frequency dynamic loads are more suited to flexible adhesives. This phenomenon is due to the ability of a flexible adhesive to absorb and flex with dynamic loads, whereas higher strength adhesives will not flex, which may lead to substrate or joint fatigue over time. On the one hand, assemblies with high vibration may need a more flexible adhesive to absorb energy without failing. On the other hand, a high-strength product would provide a higher adhesive strength but would not have the ability to absorb energy or accommodate movements and may become fatigued or cause unnecessary stress in the substrate. The flexibility of the adhesive, and its ability to absorb energy, is particularly important when engineering joints with materials that may become work-hardened, such as aluminium.