3.1.2 Weight Considerations and Strength Improvements
Reducing the overall weight of an assembly, or lightweighting, involves using advanced materials and engineering methods to enable structural elements to deliver the same or enhanced technical performance while using less material. The concept has been extensively explored and utilised in many industries, from automotive applications to fashion and packaging, and it offers significant potential performance and efficiency gains.
Lightweight materials have developed into a crucial success factor for resource efficiency in numerous industries as weight reduction leads to lower fuel or energy consumption in almost all applications. In the aerospace industry, multi-substrate bonding solutions provide up to a 30% weight reduction compared to components made solely of steel or aluminium. Therefore, durable and robust bonds, optimised curing speeds and the possibility of bonding various materials are invaluable in such industries. Matrix resins allow for the production of exceptionally lightweight fibre-reinforced composite structural components; these adhesives are used to bind fibre matrices under heat and pressure to form an extremely robust yet light finished material.
The automotive industry uses the most lightweight materials, mainly out of necessity, as manufacturers must respond to increasingly strict emission regulations. For electrically powered cars, efficient but heavy batteries must be used in lightweight cars to maximise the potential range and satisfy consumers who are used to the convenience of fossil fuel-powered vehicles. Modern adhesives and composite materials reduce the weight of cars by up to 15% versus common all-metal (steel or aluminium) components. An example is localised reinforcement within pillars and designed gaps using high-performance structural foams.
A hybrid vehicle structure consists of a fibre-reinforced frame or carrier – e.g. injection moulded glass-filled PA resin – and structural foam injected at predefined sections. The foam expands during a heat curing process (used for curing chassis-protecting e-coat systems) and creates a stiff connection between the hybrid structure and the body-in-white unit. Compared to all-metal structures, the design freedom and efficient processing offered by fibre reinforced plastics (FRP) and foam materials facilitate the adaptation of each structure to the required geometry, with locally stiffening foam ribs added precisely where needed. The structural foam used in such hybrid designs is an epoxy-based material that delivers high strength and stiffness at a low weight-to-volume ratio.
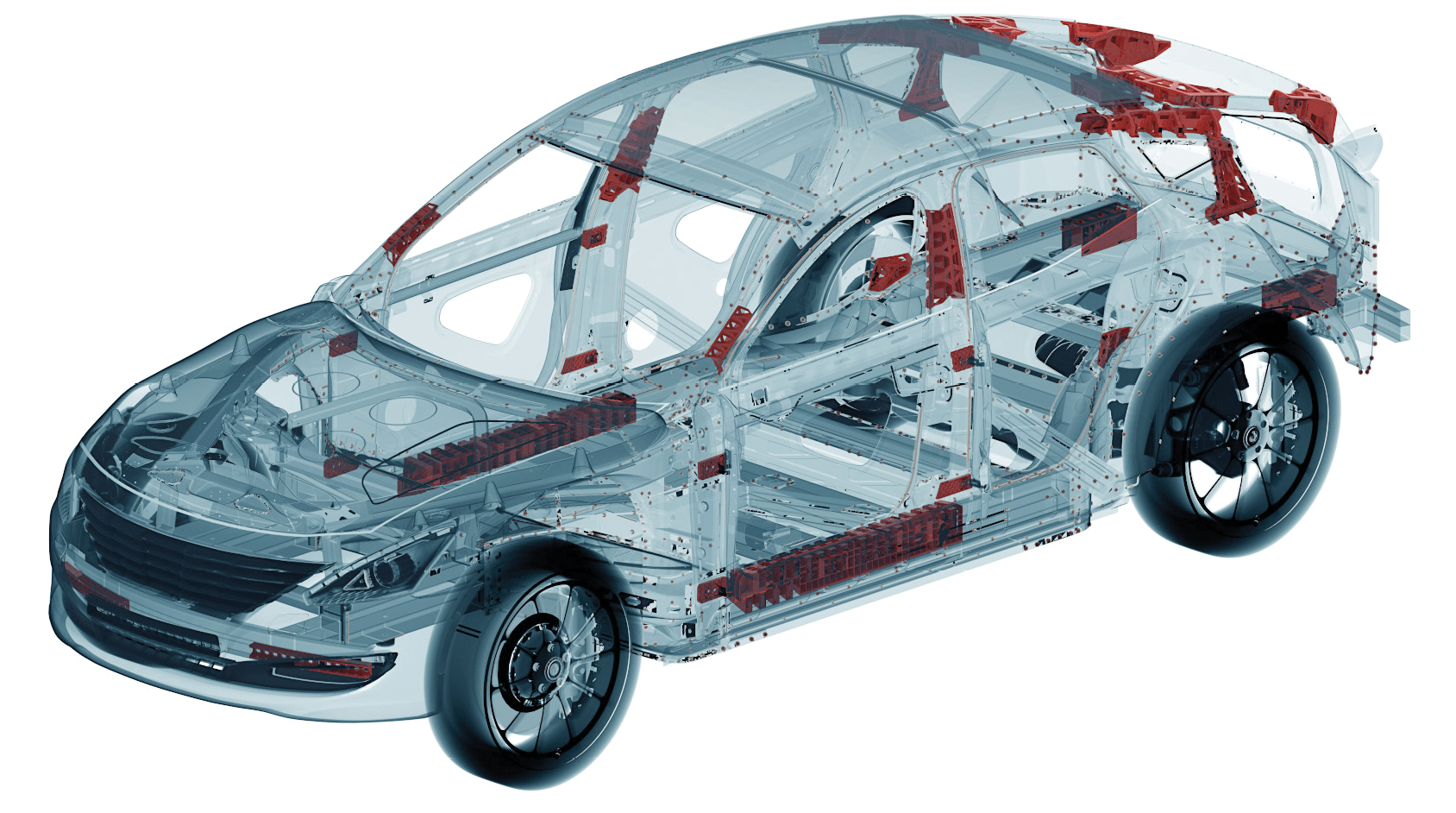
Lightweighting is also essential in the aerospace and shipbuilding industries. In heavy seas or turbulent weather conditions, ships and aeroplanes are exposed to tremendous forces and violent impacts. Therefore, it is critical to correctly specify a rigid or elastic adhesive for a given application. Unlike mechanical joints, such as rivets or screws, adhesive bonding can accommodate variable loading and prevent components or surfaces from separating due to the two-dimensional transmission of force. In addition, the adhesive may provide a vibration-damping effect, which in turn increases passenger comfort. For example, windows are no longer made of glass, but PC; these plastic windows are bonded in place using strong and flexible adhesives.
Over the lifetime of a ship or aircraft, the long-term stability of a multi-material lightweight construction achieved using adhesive bonding technologies dramatically reduces its fuel consumption and carbon dioxide (CO2) footprint. As previously discussed, adhesives can also improve manufacturing efficiency, resulting in a more sustainable and eco-friendly overall process.
Adhesive bonding strengthens the overall assembly: bonding offers several advantages over mechanical joining methods, such as welding, rivets, nuts and bolts, and crimps. Mechanically joined assemblies are usually expensive due to the following factors:
- Higher component costs (nuts and bolts, rivets, equipment)
- Additional processes (drilling holes for nuts and thread cutting)
- Need for skilled labour (welder, grinder)
- Secondary finishing operations (grinding, polishing)
Nevertheless, adhesive bonds can join dissimilar substrates with differing coefficients of thermal expansion, are invisible in an assembly and can bond and seal in one step. The most important advantage of adhesive bonds is that they can evenly distribute the stress over a broad area rather than concentrating it in a small area, thus reducing stresses on the joint. The structural stress is concentrated around the rivets in the riveted assembly, even though a greater contact area between the parts is available. However, the stress is distributed over the entire contact area between the two parts in a bonded assembly (this concept is covered in detail in Section 4). In many cases, an assembly joined using traditional methods must be strengthened around the joint to avoid failure during the operation.