5.1 Adhesive Joint Design
5.1.1 Assemblies and Joint Stress Distribution
Alternative joining techniques, such as welding or riveting, have specific benefits in certain situations, such as extreme temperatures and harsh chemical environments, where adhesives may not be suitable. However, in nearly all other circumstances, adhesives can provide an exceptionally robust and reliable solution if the assembly is designed correctly. Adhesive assemblies excel with the uniform distribution of stress, and a well-designed assembly will often be stronger than many alternative joining methods such as riveting or bolting.
As shown in Figure 104, the stress distribution of adhesive bond lines is significantly more uniform than bolting or even welding. The even stress distribution exhibited by a correctly designed bond line has several advantages. It will primarily help prevent substrate fatigue and create a stronger, more impact-resistant assembly.
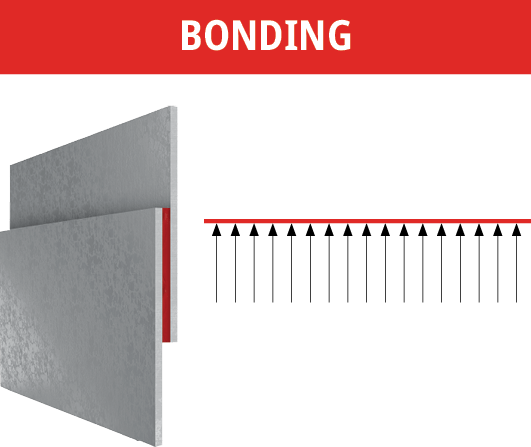
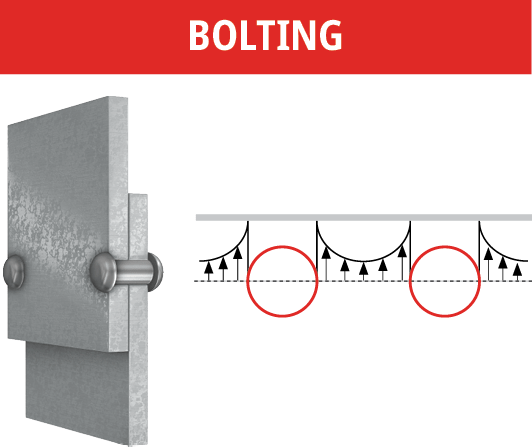
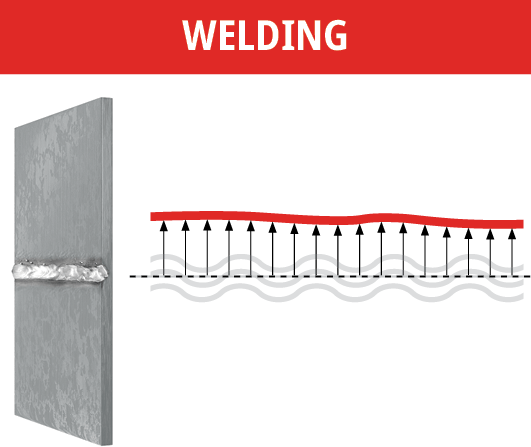
Adhesives can be used successfully in a wide range of processes and can be integrated into nearly any manufacturing environment. As shown in Table 16, adhesives can offer various benefits that many alternative joining methods do not, such as invisible application or increased aesthetics, better stress distribution, uniform strength across the assembly, no surface/substrate damage, no corrosion and decreased parts inventory. While commonly used to bond similar substrates, adhesives are often the only choice for bonding dissimilar substrates.
CONTAINMENT | ADHESIVES | BLIND RIVET | WELDING | SCREW | NUT, BOLT & WASHER | TUBULAR AND SEMI-TUBULAR RIVET | SOLID RIVET |
Invisible in application | |||||||
Stress distribution | |||||||
High tensile & shear strength | |||||||
Different materials | |||||||
Can join different materials | |||||||
High and low temperature resisitance | |||||||
No hole required | |||||||
Vibration resistant | |||||||
Uniform strength | |||||||
All work done from one side | |||||||
Eliminates heat distortion | |||||||
Clean appearance/aesthetics | |||||||
Fastens in one operation | |||||||
Joins without bulky equipment | |||||||
Pressure-tight (without seal) | |||||||
Tools readily available | |||||||
Can be installed without power | |||||||
Small capital investment | |||||||
Minimum equipment needed | |||||||
Tamper resistant | |||||||
Holds plastic | |||||||
Easy alignment of work surfaces | |||||||
Prevents surface damage | |||||||
Minimum back-up space | |||||||
Flush finish | |||||||
Wide grip range | |||||||
Low parts inventory | |||||||
Eliminates equipment adjustment | |||||||
Requires minimal set-up time |